鋰電池電解液是電池性能的核心材料,其合成過程需在高壓(通常5~15MPa)、高溫(80~150℃)條件下完成,對反應(yīng)設(shè)備的安全性與效率提出了雙重挑戰(zhàn)。微型高壓反應(yīng)釜憑借體積小、傳質(zhì)效率高、控溫精準(zhǔn)等優(yōu)勢,成為電解液合成的理想選擇,但其安全性與效率的平衡仍是技術(shù)優(yōu)化的關(guān)鍵。
?一、安全性:高壓環(huán)境下的風(fēng)險防控
微型高壓反應(yīng)釜在電解液合成中需應(yīng)對高壓氣體(如CO?、EC溶劑蒸汽)?與高活性鋰鹽(如六氟磷酸鋰)?的雙重風(fēng)險。
?1.耐壓結(jié)構(gòu)設(shè)計:采用316L不銹鋼或鈦合金殼體,通過有限元分析優(yōu)化壁厚與法蘭連接結(jié)構(gòu),確保承壓能力達20MPa以上(遠高于常規(guī)工作壓力),避免超壓破裂風(fēng)險;
2.?密封技術(shù)升級:金屬復(fù)合密封圈(如不銹鋼+石墨層)與法蘭面鏡面拋光(Ra≤0.8μm)結(jié)合,可承受高壓循環(huán)(≥1000次)而不泄漏,防止電解液揮發(fā)或氫氟酸(HF)腐蝕;
?3.智能泄壓系統(tǒng):集成爆破片(閾值設(shè)定±0.5MPa誤差)與電磁泄壓閥,當(dāng)壓力傳感器檢測到異常升高時,0.1秒內(nèi)啟動泄壓,避免超壓爆炸。
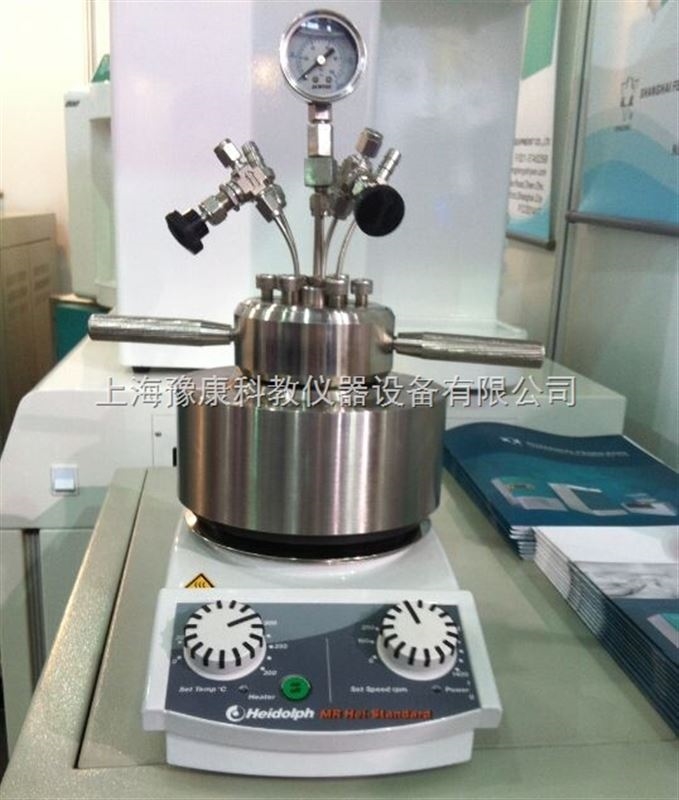
?二、效率:高壓-高溫協(xié)同下的反應(yīng)優(yōu)化
電解液合成效率取決于傳質(zhì)速率與反應(yīng)均勻性,微型高壓反應(yīng)釜通過以下設(shè)計實現(xiàn)突破:
?1.微通道攪拌槳:采用渦輪式+錨式復(fù)合攪拌結(jié)構(gòu),槳葉表面激光雕刻微米級溝槽,可提升局部湍流強度30%以上,使鋰鹽與溶劑的混合時間從傳統(tǒng)反應(yīng)釜的30分鐘縮短至15分鐘;
2.?高精度溫控系統(tǒng):內(nèi)置PT100溫度傳感器與PID控制器,控溫精度達±0.5℃,避免局部過熱導(dǎo)致電解液分解(如EC脫水生成乙烯碳酸酯副產(chǎn)物);
3.?壓力-溫度耦合控制:通過PLC實時調(diào)節(jié)加熱功率與泄壓閥開度,在保證安全的前提下維持最佳反應(yīng)條件(如10MPa/120℃),使電解液關(guān)鍵指標(biāo)(離子電導(dǎo)率、水分含量)達標(biāo)時間縮短20%。
?三、未來方向:智能化與標(biāo)準(zhǔn)化
未來微型高壓反應(yīng)釜將向智能化監(jiān)測與工藝標(biāo)準(zhǔn)化發(fā)展:
1.集成在線拉曼光譜或電化學(xué)阻抗傳感器,實時監(jiān)測電解液合成中的副產(chǎn)物生成與反應(yīng)終點;
2.制定高壓反應(yīng)釜安全操作規(guī)范(如壓力波動預(yù)警閾值、密封件更換周期),推動行業(yè)安全水平提升。
微型高壓反應(yīng)釜通過結(jié)構(gòu)創(chuàng)新與智能控制,在鋰電池電解液合成中實現(xiàn)了安全性與效率的動態(tài)平衡,為高能量密度電池的研發(fā)提供了可靠保障。隨著材料科學(xué)與自動化技術(shù)的進步,其應(yīng)用潛力將進一步釋放。